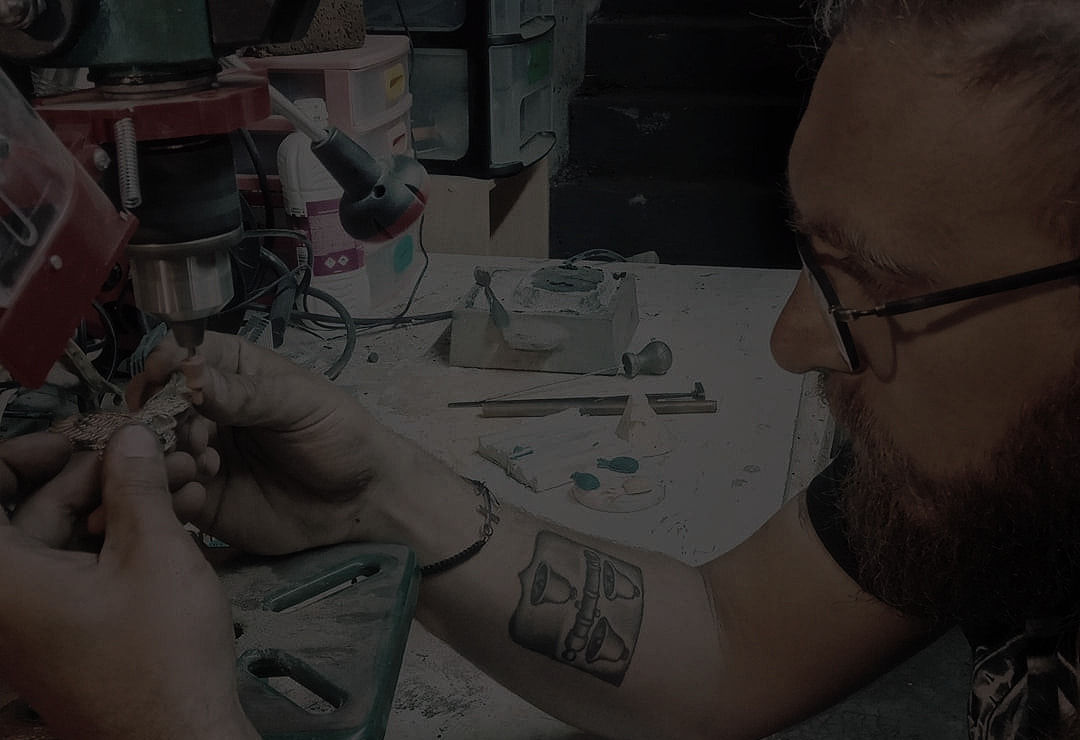
De nombreuses possibilités sont applicables en Fonderie artisanale, mais voici un résumé de mon processus standard :
- Pour toute nouvelle réalisation, je commence par créer un fichier 3D numérique de la pièce à réaliser via un logiciel de CAO (Conception Assistée par Ordinateur).
- Dans un premier temps, le fichier 3D va me permettre de communiquer sur les détails du projet et les finitions possibles (visualisation des différents volumes, des zones polies, satinées, laquées...)
- Une fois le design validé, je créée un modèle en résine via mon imprimante 3D DLP (procédé de stéréolithographie, c'est à dire avec de la résine liquide polymérisée couche par couche aux UV).
- Le modèle est ensuite retouché et ébavuré à la main pour permettre le moulage.
- Je réalise un moule en sable haute précision au contact du modèle puis en sable silico-argileux en remplissage. Tout le système de coulée par lequel le métal va alimenter la pièce, est conçu selon les règles du métier puis taillé à la main dans le sable.
- Enfin, dans un four à gaz, je porte le bronze à une température de 1250°C (permettant ainsi de le passer à l'état liquide avec une surchauffe de sécurité) puis le coule dans le moule.
- Restera ensuite la récupération de la pièce, sa séparation du système de coulée, l'ébavurage, meulage ponçage et finition.
Chaque moule est détruit après la coulée et le sable sera recyclé pour de futures fabrications (Et la Planète nous dit merci !).
Cela fait partie de la beauté du métier et du caractère unique de chaque pièce obtenue !

