

La Fonderie c'est quoi ?
Pour faire simple, on appelle "Fonderie" le métier
qui consiste à mettre en forme un matériau métallique
en le portant à l'état liquide puis en le coulant dans un moule.
A ne PAS confondre avec la Forge ! Ce sont 2 métiers complètement différents;
En Forge, le métal n'est pas fondu, il est ramolli puis déformé mécaniquement.
Historiquement au Moyen Age, les Forgerons pouvaient également pratiquer la Fonderie mais c'est bien le cinéma et la culture populaire qui ont mis la forge sur le devant de la scène (car plus visuel peut être) au détriment de la Fonderie, aujourd'hui confondue voir oubliée.
TRES BREF résumé de l'histoire de la Fonderie :
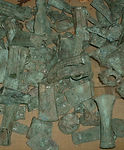

.jpg)


La Fonderie est un levier majeur du développement de l'espèce humaine.
Dés l'antiquité (3000 ans Av J-C), l'Homme sachant déjà travailler la pierre, découvrit qu'il pouvait rendre le cuivre liquide en le chauffant dans des bas fourneaux en argile, puis le couler dans des moules pour créer de nouveaux outils et armes plus résistantes.
Rapidement, les bases de la métallurgie furent créées, avec la découvertes de nouveaux métaux (étain, Fer, Or...) puis du bronze (alliage Cuivre + Etain) permettant de diminuer la température nécessaire pour fondre.
Au fur et à mesure des ages, la Fonderie s'est diversifiée : A l'époque gallo-romaine, de nombreux ornement d'arts furent créés par Fonderie
Au Moyen-Age, la Fonderie a permis de créer des pièces mécaniques pour des assemblages toujours plus complexes, mais également des cloches pour toutes les églises du monde.
Arriva ensuite la fabrication des canons et pièces d'artilleries pour équiper les navires et les armées à l'époque de la Renaissance.
De 1760 à 1840, c'est la révolution industrielle qui provoque l'explosion du développement des métiers de la métallurgie (Fonderie, Forge, Chaudronnerie...). Durant cette période, de nombreux procédés et équipements furent inventés (dont certains toujours utilisés industriellement aujourd'hui !), afin d'améliorer la productivité et les propriétés des pièces fabriquées.
Au XXème siècle, les grandes guerres apportèrent à la Fonderie des avancées majeures grâce aux nombreuses recherches motivées par l'amélioration des équipements militaires et des moyens de les produire.
De nos jour les métiers de la Fonderie emploient environ 29000 salariés rien qu'en France dans environ 380 usines et ateliers afin de produire pour les secteurs principalement automobile, le bâtiment, les équipements mécanique, l'aéronautique et bien sûr l'Art)
(source: Forgefonderie.org).
A méditer :
Pour beaucoup, la Fonderie et la Forge sont des métiers désuets d'un autre temps, mais sans eux nous n'aurions ni voiture, ni train, ni avion, ni fusée !
Les principaux moyens de moulage :
Nous l'avons dit plus haut, la fabrication par Fonderie s'opère en portant le métal à l'état liquide.
Pour amener cette masse liquide à prendre la forme de la pièce à fabriquer, il faut la couler dans un moule ayant pour empreinte la forme de la pièce.
Il existe 2 types de moules : les réutilisables et les non réutilisables.
Les premiers sont bien souvent réservés à l'industrie car ils sont réalisés en métal, très onéreux. On peut y couler du métal (par gravité ou sous pression) plusieurs milliers de fois avant que ceux-ci ne soient trop usés pour produire des pièces correctes.
Les seconds sont détruits à chaque coulée pour récupérer la pièce. Les moules peuvent être réalisés en sable ou en plâtre qui sont 2 matériaux très réfractaires qui résistent aux hautes températures de la coulée.
Ci après, quelques procédés de moulage non réutilisables :
- Le moulage sable "traditionnel" (le cœur de mon savoir-faire, que je partage sur ce site) :
Nécessite la fabrication d'un modèle en bois, plâtre, résine ou tout autre matériau (plus ou moins une réplique de la pièce à fabriquer).
On vient disposer un cadre (appelé "châssis") autour du modèle afin de contenir le sable.
Ensuite, on rempli le châssis avec du sable, ce qui va recouvrir le modèle.
Pour avoir une certaine cohésion, le sable doit être durci;
De nombreux procédés existent pour le durcissement selon les additifs qui enrobent les grains de sable.
Le sable peut durcir mécaniquement (en appuyant dessus comme pour faire un château de sable), par cuisson, par réticulation de résine, ou même par mise sous vide !
Une fois le sable durci, on peut démouler le modèle qui laisse une empreinte dans le sable de la pièce à fabriquer.
- Le moulage cire perdue (facilite souvent les choses donc je partage également) :
Pour ce procédé, le modèle doit obligatoirement être réalisé en cire, et celui ci ne sera pas réutilisable.
le moule est réalisé dans un cylindre (ou "flasque") en métal.
On place le cylindre autour de la cire et on coule un plâtre réfractaire qui vient enrober la cire.
La cire prisonnière du plâtre est fondue pour être évacuée en plaçant le moule dans une étuve.
Celle ci en fondant laissera derrière elle sa propre empreinte dans le moule.
Le moulage cire perdue est un peu plus simple à mettre en œuvre car on ne démoule pas le modèle. Toutefois, celui ci génère beaucoup de déchets de plâtre après coulée. A contrario, de nombreuses solutions existent pour réutiliser le sable.
- Les procédés "Exotiques" :
Il existe d'autres procédés comme le "lost foam" où le modèle en polystyrène est laissé dans le moule en sable puis brûlé par le métal lors de la coulée, ou bien le moulage à la trousse où on met en forme une motte de sable avec un couteau monté sur un axe (pour fabriquer les cloches par exemple) ou encore très récemment, les moulages par impression 3D de sable.

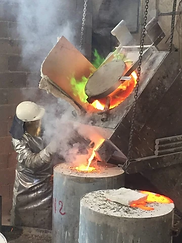
![DSCN0282 [1600x1200].JPG](https://static.wixstatic.com/media/20a6e2_55fd78e2177647d386afb1da34878f55~mv2.jpg/v1/fill/w_319,h_239,al_c,q_80,usm_0.66_1.00_0.01,enc_avif,quality_auto/DSCN0282%20%5B1600x1200%5D_JPG.jpg)


Les principaux moyens de fusion :
Le but d'un four est de porter le métal à une température suffisante pour le rendre liquide afin de le couler.
Chaque métal et alliage a sa propre température de coulée, ce qui influencera le choix du moyen de fusion.
Les fours électriques :
- à résistances : le rayonnement va chauffer le creuset contenant le métal (très utilisé pour les métaux à bas point de fusion)
- à arc : un fort courant parcours des électrodes en graphite qui en affleurant le métal, créé un arc électrique dont l'énergie va faire fondre le métal (très utilisé en aciéries et dans les filières de recyclage)
- à induction : Une bobine est parcourue par un courant, générant un champ magnétique accompagné d'un échauffement du métal à portée.

Les fours à combustible :
- à gaz (que je propose de vous apprendre à fabriquer) ou à fioul : le combustible est injecté dans un brûleur. En général, le brûleur est orienté vers le creuset et non directement vers le métal à fondre afin de limiter l'oxydation de celui-ci (sauf cas particulier des fours "réverbères")
- à charbon ou à coke (que je vous apprendrait à fabriquer également !) : des boulets de charbon ou de coke sont disposés autour du creuset. Après allumage, de l'air est soufflé en continu afin d’attiser les braises et augmenter la température.
-le Cubilot : Héritage de la révolution industrielle, il est encore utilisé aujourd'hui dans certains ateliers et son fonctionnement est passionnant.
C'est une colonne que l'on rempli de coke, de métal et de chaux. Une fois allumé, de l'air est soufflé par des tuyères afin d'attiser les braises. Le métal va fondre en gouttelettes qui vont se charger en carbone en ruisselant sur les boulets de coke avant de s'accumuler au fond de la cuve en contrebas.
Lorsqu'il y a assez de métal dans la cuve, on vient percer (ou "piquer") le bas du four pour que le métal s'en échappe vers un creuset.
C'est LE moyen de fusion le plus noble et le plus complexe à maitriser. Il est également connu pour donner la fonte de la meilleure qualité (notamment grâce à la recarburation sur les boulets de coke).
Un point sur LE coke (nom MASCULIN) : c'est un combustible de synthèse inventés par les anglais à l'air industrielle pour pallier au manque de ressources en bois de leur ile. Le coke est issu de la houille, une roche minée puis préparée dans une cokerie (il est également très prisé des artisans forgerons car il a un meilleur rendement que le charbon, pour un pouvoir calorifique quasi identique)

