

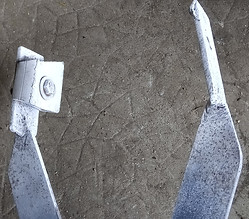
S'équiper pour la fusion :
Disclaimer : La Fonderie et la fabrication d'un four de fusion sont des travaux dangereux.
Il est indispensable de prendre toutes les précautions nécessaires pour éviter toute blessure, incendie ou explosion.
Vous êtes seul-e responsable de la sécurité de vos installations, ce site n'étant exposé qu'à titre informatif !
le matériel de Sécurité (IMPORTANT) :
Les gants anti chauffe :
En coton, en cuir ou en croute de vachette, ceux ci doivent comporter le sigle de la flamme EN 407.
Préférez les gants en croûte qui offrent une meilleure protection que le cuir léger, au détriment de la dextérité.
Attention, la simple apposition du sigle ne suffit pas, il faut également choisir votre gant en fonction du code attenant à ce sigle.
Le code est constitué de 6 chiffres dont le tableau ci dessous vous expose la signification (source : edc-protection.com):
Pour faire simple : plus les différents chiffres seront proches de 4 (maximum), mieux vous serez protégé !
Le tablier de cuir :
Permet la protection de quasiment tout l'avant du corps contre les rayonnements et les projections.
Les guêtres :
Assure la meilleure protection contre les projections de métal fondu qui pourraient se loger dans un pli du pantalon ou entre votre cheville et la chaussure.
La pince à creuset :
Doit être adaptée à la taille de votre creuset, j'ai fabriqué la mienne par soudure avec des fers plats, mais on peut aussi en trouver auprès des fournisseurs spécialisés (EPMF) ou sur mesure chez un chaudronnier
vous pouvez reproduire la forme ci dessous. La courbure permet une fermeture de la pince sur le creuset lorsque les poignées sont serrées, on peut donc tenir le creuset avec les 2 poignées dans une seule main :
J'ai ajouté une entretoise sur l'un des mors de la pince afin
de pouvoir prendre des creusets de plus petite dimension :
La lingotière :
C'est un moule ouvert (donc sans DESSUS, car plus rapide à réaliser), dans lequel vous pourrez couler le métal restant dans votre louche ou creuset, une fois la coulée de vos pièces terminée.
En effet, il faut absolument éviter de laisser du métal se solidifier dans la louche ou le creuset, car lors de la fusion suivante, celui va fortement détériorer son contenant en se dilatant lors de la montée en température.
La lingotière peut être permanente en métal (plus chère) ou tout simplement une simple forme creusée dans un moule en sable (plus rapide, économique et réutilisable jusqu'à une dizaine de fois).
Nul besoin de réaliser des lingots en belle forme de lingot d'or (même si c'est joli), le seul objectif est de pouvoir couler puis récupérer le métal en vue d'une fusion suivante !
Fabriquer son four de fusion, réunir le matériel :
Ci dessous, je vais vous exposer une méthode simple pour la réalisation d'un four (gaz ou charbon) pouvant atteindre des températures de 1200°C (vous permettant la fusion de la totalité des métaux usuels sauf les ferreux).
Le Bâti :
C'est le squelette métallique de votre four qui maintiendra le béton en place. Vous pouvez utiliser un tubage de cheminée ou un fût de 200L en acier. Il est possible d'utiliser des tubages en aluminium car grâce au béton réfractaire, la température du bâti ne dépassera pas les 40°C.
Le béton :
Pas de secret pour le béton, en acheter du tout fait, réfractaire. Comptez 50kg de béton pour réaliser un four dans un bidon de 200L.
Il vous sera possible d'utiliser :
-Du béton à couler (nécessitera de créer des gabarits en polystyrène pour que le centre du four soit creux.
-Du mortier (peut se couler comme le béton mais le résultat sera plus friable)
-Du béton à damer (la meilleure solution selon moi car on peut l'appliquer à la main et le travailler comme une glaise sans fabriquer de gabarits ou coffrages)
Le brûleur (Version four à gaz uniquement) :
On trouve des brûleurs à gaz "pour forge" en vente sur internet.
Choisissez une puissance de 20KW-H (ou 80000 BTU en unité anglaise).
Il est aussi possible de le fabriquer soi même selon la méthode du brûleur YACO (voir méthode sur ce site: https://couteliers.com/archives/bruleur/index.html )
Attention, il existe des versions atmosphériques ou à enrichissement par air pulsé. Dans le premier cas (à gauche ci-dessus) on pourra fondre sans électricité, dans le second cas (à droite ci-dessus), un compresseur d'air sera nécessaire (mais la conso de gaz diminuera !).
La soufflerie (Version four à charbon uniquement) :
On peut trouver des souffleries électriques dans le commerce, ou bien le plus simple reste le vieux sèche cheveux (à régler sur air froid pour ne pas griller sa résistance au bout de 10 minutes) !
Evitez les souffleries manuelles comme on trouve sur les forges. En effet, celles-ci sont prévues pour des chauffes ponctuelles (à moins que vous n'ayez la motivation de tourner une manivelle en continu pendant les 30 à 50 minutes que dureront la fusion !)
La buse d'air (Version four à charbon uniquement) :
En métal d'une longueur de 15cm environ, elle doit pouvoir s'adapter à la sortie de la soufflerie (ou sèche cheveux) afin de conduire l'air soufflé à l'intérieur de la chambre de combustion sans prendre le risque de brûler la soufflerie.
Vous pouvez utiliser un tronçon de conduite en zinc, en acier ou en aluminium (l'air frais apporté par la soufflerie empêchera la fusion de la conduite pendant la chauffe).
Si possible, déformez légèrement la buse en forme de cône ou de bec de canard afin d'accélérer le flux d'air dans la chambre de combustion.
Le creuset :
Choisissez un creuset en graphite, avec une contenance adaptée (un creuset trop gros réduira le rendement et augmentera les temps de fusion et l'oxydation !).
Attention, le graphite est un matériau très fragile qui craint les chocs mécaniques, thermiques et l'humidité.
Un creuset neuf en graphite coûte environ 150€ selon la contenance, mais si vous en prenez soin, il supportera plus d'une centaine de fusions !
La brique de siège :
En céramique réfractaire, celle-ci a pour but de surélever le creuset pour que la flamme puisse en chauffer le dessous et améliorer grandement le rendement.
Egalement, cette brique évite au creuset de coller au fond du four lors de la fusion.
Elle n'est pas très chère et on en trouve chez EPMF ou chez les fournisseurs de matériel pour céramistes.
Pour ma part, j'utilise un tronçon en graphite issu d'une électrode pour four de fusion à arc.
Fabriquer son four de fusion, choisir le combustible :
Pour le four que je vous propose de fabriquer, 2 choix s’offrent à vous :
Le charbon ou le coke :
Avantages : -Plus traditionnel. Avec la fumée les grandes flammes et les odeurs de charbon, cela donne des fusions spectaculaires !
-Le charbon et le coke pourront également servir pour une forge (d’ailleurs en enlevant le creuset, votre four fera un parfait brasier pour la forge !)
-Le charbon est particulièrement simple à se procurer dans toutes les grandes surfaces.
-Le coke s’obtient auprès de fournisseurs spécialisés ou forgerons. Contrairement aux idées reçues, le coke n’a pas un pouvoir calorifique très supérieur au charbon ; la différence c’est le rendement ! En effet, le coke brûlera plus longtemps donc moins de consommation et moins besoin de recharger !
Inconvénients : -nécessite constamment un apport d’air soufflé pour aviver les braises (donc une soufflerie ou sèche-cheveux à brancher sur l’électricité).
-La fusion nécessite une présence constante pour surveiller le niveau de charbon, le tasser dans la chambre de combustion et refaire le niveau régulièrement (c’est un peu moins le cas avec le coke).
-Selon la qualité du charbon et le débit d’air, de nombreuse petites braises peuvent s’envoler constamment, il faut donc protéger les lieux et les personnes aux abords du four (avant la fusion, ne pas hésiter à arroser le sol autour du four pour éviter tout incendie !)
Avec du charbon, je suis à 7kg par fusion. Cela revient à environ 10€/fusion
(cela dépendra de la puissance de la soufflerie et de la quantité à fondre).
Le gaz :
Avantages : -Des fusions en autonomie n’importe où sans besoin de courant électrique !
-Le gaz est plus simple à maîtriser car il n’y a qu’à tourner la vanne du manomètre pour jouer sur la puissance du four.
-Les alentours du four seront plus propre après la fusion car il n’y a pas de dégagement de cendres.
-Moins d’actions de rechargement que pour le charbon ; On tourne la vanne, on allume et on patiente !
Inconvénients : -En raison de la décompression du gaz, le butane a tendance à geler et perdre en pression au cours de la fusion (surtout en hiver). Préférez lui le propane, plus cher mais fonctionnel par tout temps et toute durée.
Si vous n’aviez pas le choix que d’utiliser du butane, une astuce contre le gel est d’immerger la bombonne de gaz dans un seau avec 10cm d’eau froide ou tiède pour atténuer le phénomène.
-Le gaz nécessite une bouteille consignée à considérer comme un investissement (mais on peut en trouver des vides d’occasion pour économiser sur la consigne).
-Il faudra vous procurer des raccords avec manodétendeur de pression à brancher directement sur la bouteille, auprès de fournisseurs de matériel de forge ou céramique (surtout pas de détendeur standard car la pression n’est pas réglable et la puissance délivrée est bien trop faible !)
Pour la conso, je suis à 25 fusions pour 35kg de propane. Avec une recharge de 100€, cela revient à 4€/fusion (cela dépendra de la puissance de votre brûleur et de la quantité à fondre).
Fabriquer son four de fusion, méthode et conception :
La conception du four de fusion est très simple; C'est un tube en béton entouré d'une enceinte métallique avec un trou pour y passer un brûleur ou une soufflerie.
1/ Nettoyez le bâti : Celui ci doit être propre sec et dégraissé.
2/ Coulez un béton réfractaire ou masse à damer dans le fond du bâti (3 à 5 cm d'épaisseur minimum) : On appelle cela "la sole" du four.
3/ Après séchage, disposez la brique de siège et le creuset afin de vous rendre compte de la position de ces derniers dans le bâti.
4/ Avec une disqueuse, découpez l'arrivée d'air/gaz selon le plan ci-dessus.
La dimension et la position du trou doivent permettre de passer le brûleur ou la buse d'air et de l'orienter de manière à ce que :
- le flux d'air ou de gaz TANGENTE le côté du creuset (voir schéma plus haut), avec une inclinaison légèrement vers le bas (Comme cela en cas de fuite, le métal ne pénètrera pas dans le brûleur ou la buse d'air).
-Le flux d'air ou de gaz arrive sur la partie basse du creuset
5/ Enlevez le creuset et la brique de siège et montez les parois réfractaires du four sur tout le pourtour jusqu'à 5cm au dessus du creuset.
Pour cela, vous pouvez plaquer de la masse à damer à la main, ou couler un béton (nécessitera de créer un gabarit cylindrique en polystyrène à enlever après séchage).
En général, comptez une épaisseur de réfractaire mini de 30mm.
Toutefois selon la taille du creuset, l'espace entre celui ci et la paroi de béton doit être comprise entre 40 et 70mm.
(assez large pour y passer le charbon, assez étroit pour limiter les déperditions de chaleur)
6/ Ajoutez du mortier, de la masse à damer ou du béton épais autour du brûleur/buse d'air afin d'assurer son maintien et son étanchéité au niveau du perçage.

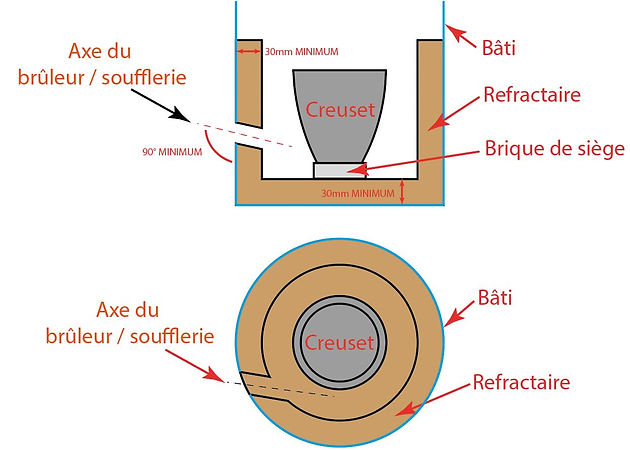

